Introduction
Imagine this: a bustling Melbourne warehouse where heavy machinery rumbles across the floor, workers rush to meet deadlines, and chemicals spill without warning. Now picture the floor — cracked, stained, and slippery. This is a daily reality for many warehouse managers, leading to costly repairs, unsafe working conditions, and constant operational disruptions.
In Melbourne, where industrial spaces are vital to the economy, flooring isn’t just an aesthetic choice; it’s a critical factor in operational efficiency, safety, and longevity. Whether you’re managing a logistics hub, manufacturing plant, or distribution center, selecting the right flooring solution can significantly impact your bottom line.
Enter epoxy flooring — the ultimate solution to warehouse flooring challenges. Known for its durability, chemical resistance, and slip-resistant properties, epoxy coatings provide Melbourne warehouses with a cost-effective, long-lasting floor solution. In this guide, we will explore the numerous benefits of epoxy flooring, how to install it, and why it is the best option for warehouses looking to improve both functionality and aesthetics.
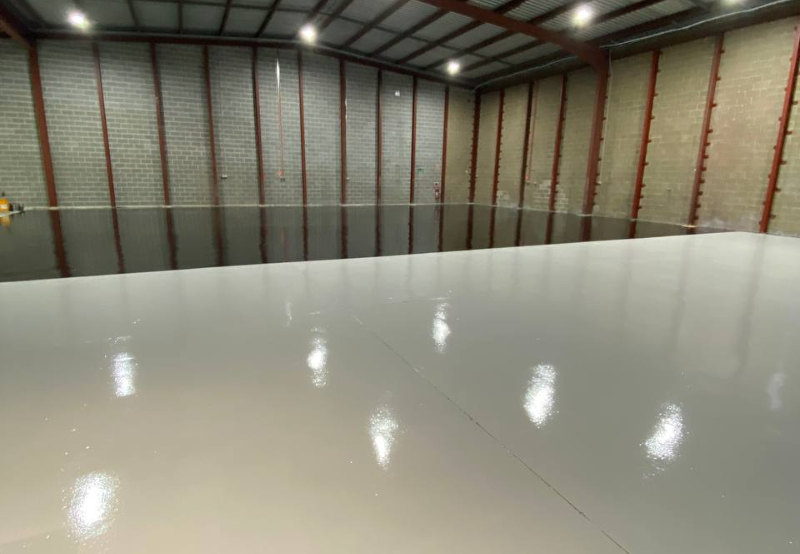
Understanding the Benefits of Epoxy Flooring
Durability and Longevity: The Lifespan of Epoxy Floors
When it comes to industrial floors, durable flooring is non-negotiable. Epoxy coatings are renowned for their impressive lifespan, often lasting 10 to 20 years with proper maintenance. Unlike traditional concrete floors, which can crack, stain, or wear down over time, epoxy flooring forms a tough, seamless surface that resists the rigors of heavy foot traffic, machinery movement, and extreme temperatures.
Epoxy floors can withstand high-impact wear, making them an excellent choice for environments like warehouses where machinery and equipment are constantly in motion. The long-lasting flooring not only reduces the need for frequent replacements but also improves overall cost-efficiency by minimizing downtime.
Chemical Resistance: Protecting Your Warehouse Investment
In warehouses, chemical spills are an unavoidable risk. From oils and fuels to cleaning agents and solvents, exposure to hazardous substances can deteriorate floors, causing them to become porous, cracked, or discoloured. Fortunately, chemical-resistant flooring like epoxy is designed to withstand these tough conditions.
Epoxy coatings create a non-porous surface, preventing chemicals and liquids from seeping into the floor, which protects your warehouse investment. Whether it’s spill-resistant flooring for an automotive warehouse or protection against acidic substances in a chemical warehouse, epoxy floors are engineered to maintain their integrity and look, no matter what gets spilled on them.
Slip and Fall Prevention: Ensuring a Safe Workplace
In a fast-paced warehouse, safety is paramount. Slippery floors can be a significant hazard, leading to accidents and injuries. Epoxy floors can be slip-resistant, providing excellent traction underfoot, even in areas prone to wetness or spills.
Anti-slip flooring features are integrated into the epoxy coating process, making it a perfect choice for warehouses with high moisture levels, forklifts in constant motion, or areas where workers are frequently carrying heavy loads. By investing in safety flooring, you can reduce the risk of workplace accidents, protect your employees, and ensure compliance with health and safety regulations.
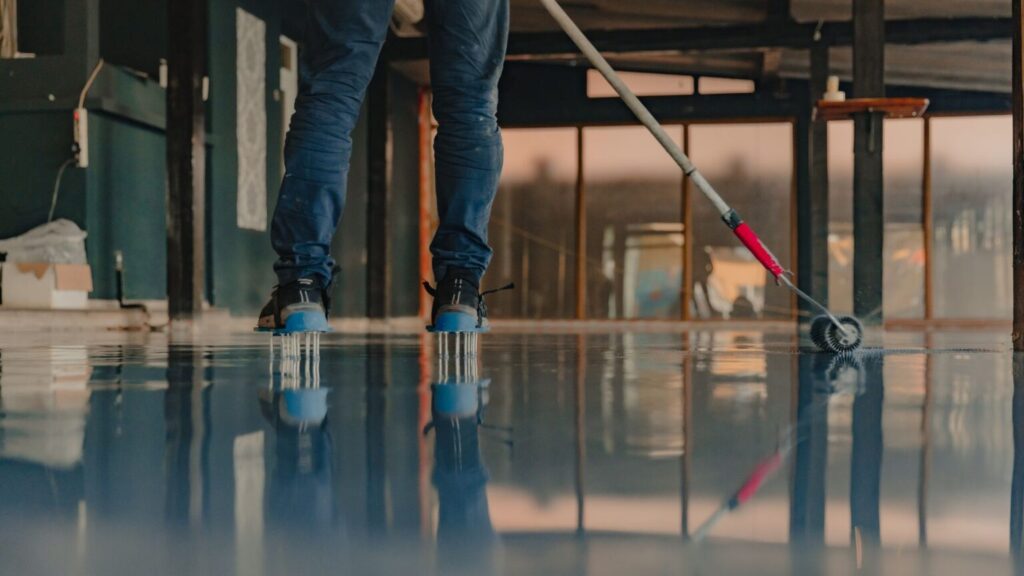
The Epoxy Flooring Installation Process
Preparing the Surface: Laying the Foundation for a Strong Floor
Before the epoxy coating is applied, the surface preparation is critical. A successful installation starts with a clean, smooth, and well-prepared foundation. This ensures that the epoxy adheres properly and creates a long-lasting, durable finish.
- Floor Cleaning: The first step is to thoroughly clean the warehouse floor. Dirt, oil, and grease can all interfere with the bonding process. Specialized floor cleaning methods, including shot blasting or diamond grinding, are often employed to remove contaminants and achieve the proper surface texture.
- Floor Repair: Cracks and holes in the floor need to be addressed before epoxy is applied. Filling in these imperfections ensures a smooth, uniform surface that allows the epoxy to cure properly.
- Floor Preparation: After cleaning and repairing, the floor is prepped with an acid wash or etching solution to enhance the epoxy’s adhesion. Without proper floor preparation, the epoxy will not bond well, reducing its effectiveness.
Applying the Epoxy Coating: A Step-by-Step Guide
Once the floor is prepared, the application of the epoxy coating can begin. This process typically involves several steps:
- Primer Application: A primer coat is applied first to ensure proper adhesion of the epoxy to the floor surface. This step helps seal the floor and gives the epoxy a strong surface to bond to.
- Epoxy Resin Application: After the primer, the epoxy resin is mixed and applied. This resin is the heart of the epoxy flooring system, providing its strength and chemical resistance. The resin is usually applied in multiple layers to ensure full coverage.
- Topcoat Application: A final topcoat is applied to provide additional protection and to enhance the floor’s aesthetic appeal. This topcoat also adds an extra layer of anti-slip properties and further increases the floor’s durability.
Curing Time and Maintenance Tips
After the epoxy is applied, curing time is essential. While the surface may feel dry to the touch in a few hours, full curing can take up to 7 days, depending on the thickness of the layers and environmental conditions. During this time, it’s critical to avoid heavy traffic or machinery use.
Once cured, floor maintenance is relatively simple. Regular sweeping and mopping will keep the floor looking new, while periodic re-coating (every few years) can restore its shine and extend its lifespan. Since epoxy floors are highly resistant to dirt and stains, maintenance is typically low-effort compared to other industrial flooring options.
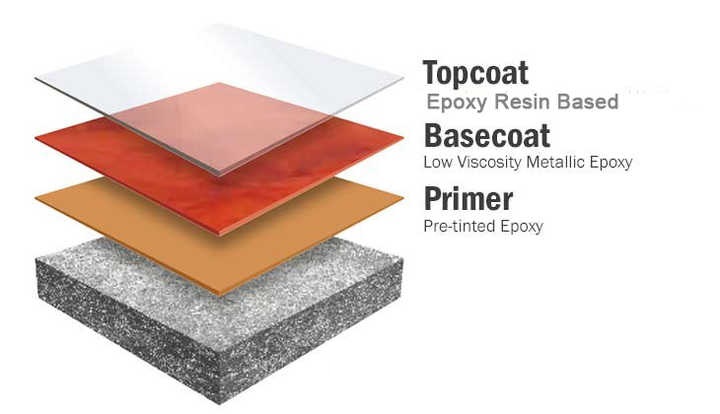
Customizing Your Epoxy Floor
Colour Options: Enhancing Your Warehouse Aesthetics
While epoxy flooring is often chosen for its practicality, it also offers a wide range of design possibilities. Coloured epoxy flooring can transform your warehouse from a utilitarian space into a visually appealing one. Customizable colour options allow you to match your brand’s colour scheme, create a visually appealing work environment, or designate specific zones within the warehouse.
In addition to aesthetics, coloured epoxy floors can also improve visibility, helping employees navigate the space more easily. For instance, decorative flooring with contrasting colours can highlight walkways, machinery areas, or hazardous zones, enhancing overall warehouse efficiency and safety.
Textured Finishes: Improving Traction and Safety
Another way to customize your epoxy flooring is through textured finishes. A textured floor not only adds aesthetic appeal but also improves traction, which is especially important for warehouses with heavy foot traffic, forklifts, or other machinery.
Non-slip flooring finishes can be tailored to meet the specific safety needs of your warehouse. Whether you need extra grip in a wet area or a more subtle texture for general use, a textured industrial floor finish ensures maximum safety without compromising on style.
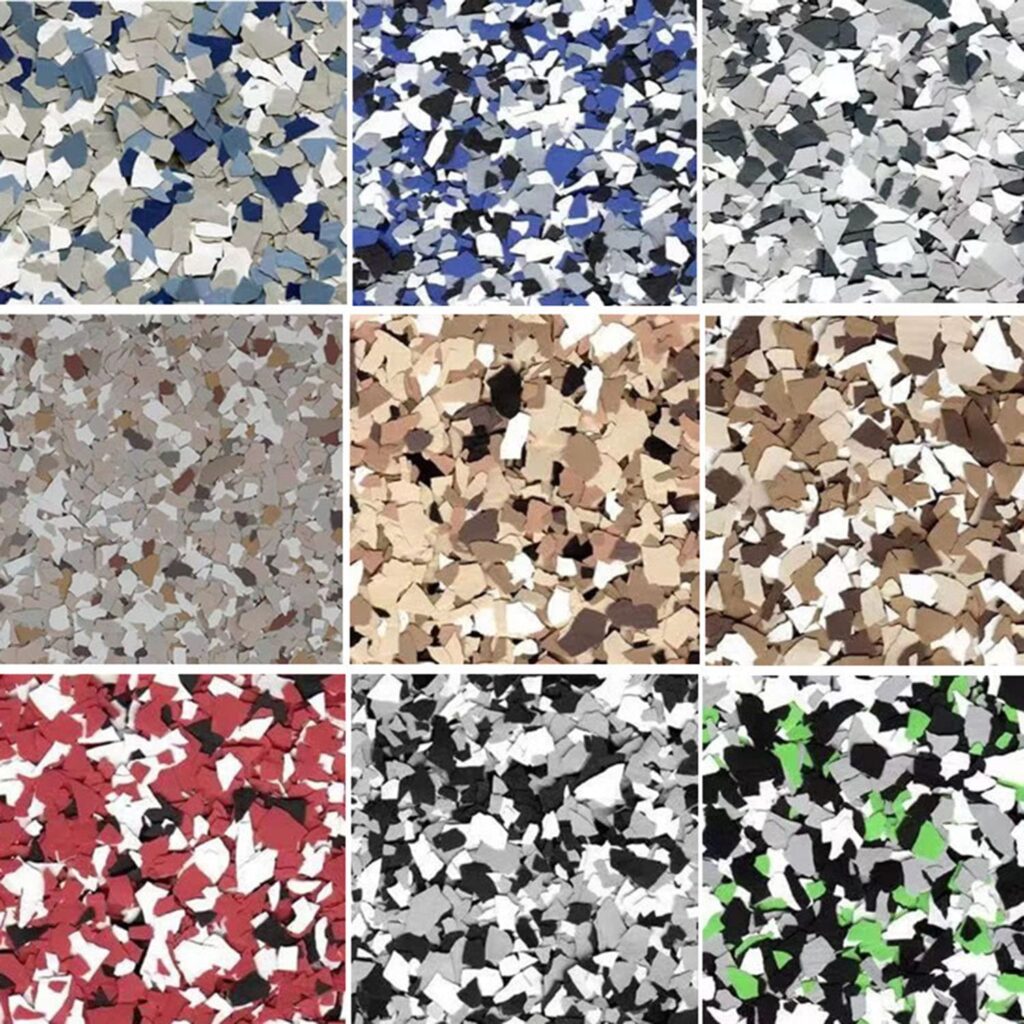
Conclusion
Epoxy flooring offers Melbourne warehouses an unbeatable combination of durability, chemical resistance, slip prevention, and aesthetic flexibility. Whether you’re looking to improve safety, reduce maintenance costs, or enhance the appearance of your warehouse, epoxy floors are the optimal choice.
If you’re ready to upgrade your warehouse flooring with a solution that stands the test of time, reach out to a local Melbourne epoxy flooring expert for a free consultation. With their expertise, you’ll have a floor that not only meets your needs but exceeds expectations.
Contact us today for a customized industrial epoxy flooring solution tailored to your warehouse epoxy flooring needs!
FAQs
FAQ 1: Is epoxy flooring suitable for all warehouse environments?
Yes, epoxy flooring is highly versatile and can be used in almost any warehouse environment. It’s particularly ideal for warehouses that handle chemicals, oils, or heavy machinery. However, certain warehouse conditions may require specialized formulations of epoxy, such as anti-static or heat-resistant versions.
FAQ 2: How long does epoxy flooring last?
Epoxy floors can last 10-20 years, depending on the quality of the installation, traffic levels, and maintenance. Proper care and periodic re-coating can extend their lifespan even further.
FAQ 3: Is epoxy flooring expensive?
While the initial investment in epoxy flooring may be higher than other options, the long-term cost-effectiveness of epoxy floors makes them a wise choice. Their durability, minimal maintenance requirements, and resistance to damage mean they will likely save you money over time.
FAQ 4: Can I apply epoxy flooring myself?
Epoxy flooring installation is a complex process that requires proper preparation, application techniques, and equipment. While DIY kits are available, hiring a professional epoxy floor coating contractor ensures a high-quality finish and prevents costly mistakes.
FAQ 5: What are the environmental benefits of epoxy flooring?
Epoxy coatings are generally low in volatile organic compounds (VOCs), making them an environmentally friendly choice compared to other industrial floor coatings. Furthermore, epoxy’s long lifespan reduces the need for frequent replacements, which contributes to less waste over time.
For more information about safety standards in industrial spaces you can check WorkSafe Victoria for warehouse safety regulations.
0 Comments